Industrial ecology
Cement manufacturing consumes large quantities of non renewable raw materials (minerals and fossil fuels). It is also an important source of CO2 emissions. In response to this environmental challenge, Lafarge has been committed to industrial ecology since the mid-70s by rethinking industrial processes to transform some industries' waste products into other industries' resources.
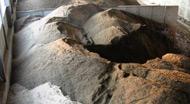
Why find uses for waste? The Group is aware of the impact of its activities on the environment. As a result, Lafarge started thinking at a very early stage about ways of reconciling industrial imperatives with the preservation of ecosystems. Adding value to waste by using it as alternative fuel or materials, makes it possible to:
Within Lafarge, the use of alternative fuels has increased by more than 30% over the last 3 years. Our objective is to have 50% of alternative fuels in our energy mix by 2020, which would represent 17.4 million tons of CO2 avoided. |
CO2 and cementWhy does the manufacture of cement produce CO2? Cement manufacturing is the source of 5% of global CO2 emissions. The cement industry is a natural producer of CO2:
Give value to emissionsLafarge has run a pilot project at its Val d'Azergues cement plant (France) to cultivate micro-algae in order to absorb CO2 emissions from the kilns. These algae can then be used as biofuel. |
Alternative fuels |
|
Kyoto ProtocolThe Kyoto Protocol aims to reduce greenhouse gas emissions on a global scale. The principle is based on varying levels of commitments for different governments. Industrialized countries have made stabilization or reduction commitments which correspond on average to a 5% reduction in their emissions for the period 2008/2012 compared with 1990. Developing countries are under no obligation but are encouraged to develop CO2 emissions reduction programs which can be used to generate credits: that is the principle of the "Clean Development Mechanism" (CDM) which involves promoting efforts in emerging countries. Industrial wasteIndustrial waste is the residue from industrial production, processing or use. Waste products from one industrial process can serve as alternative fuels and raw materials for another. Co-incineration enables enterprises to conserve fossil fuels and raw materials while serving the community by processing waste in an economical way that reduces CO2 emissions. CO2 and cementWhy does manufacturing cement produce CO2? Cement manufacturing is the source of 5% of global carbon dioxide (CO2) emissions. The cement industry is a natural producer of CO2:
|
Waste products can be very appealing alternatives to fossil fuels. In general, alternative fuels are derived from waste or byproducts from agriculture (biomass) and industry:
All of these products can be recycled as alternative fuels and burned safely in cement kilns. This approach relieves the community of the need to process this waste and helps to limit CO2 emissions. The extremely high temperatures found in cement kilns mean that the waste is totally eliminated and does not leave any residue. At present, alternative fuels account for 12% of the Group's fuel use across its cement activities. Lafarge actively participates in the Clean Development Mechanisms (C.D.M.) system initiated under the Kyoto Protocol. These mechanisms encourage the implementation of best-in-class technologies in developing countries by providing carbon credits to companies which finance sustainable development projects. For example, in:
Morocco, a wind farm provides 50% of the electricity required for the Tétouan cement plant |
Alternative materials |
|
The cement manufacturing process generates CO2 because the limestone needs to be heated to very high temperatures. This physical-chemical process of "decarbonation" produces clinker, which is then ground down. It is possible to reduce the amount of clinker in cement by using alternatives, called cement admixtures. Reducing the amount of clinker in cement offers 2 advantages:
Cement admixtures may be of:
For example, in India, the Arasmeta cement plant uses fly ash from power plants in cement manufacture. |
ClinkerClinker is the main ingredient in cement. These hardened granules are obtained by firing a mixture of approximately 80% limestone and 20% clay to a high temperature. Cement is obtained by grinding clinker and, in some cases, supplementing it with additives. PozzolanPozzolan is named after Pozzouli, a region near Naples, Italy, which is rich in volcanic ash. Natural pozzolan is a light siliceous mineral produced during basaltic volcanic eruptions. It contains silica, alumina and iron oxide (which gives it a red color), as well as lime and magnesium oxide. Pozzolan is used as a cement additive. Artificial pozzolans with the same properties as natural pozzolans can be created by heating clays, basalts or schists. Fly ashFly ash is hydrophilic (dissolves in water) and can be used as a cementitious additive. The ash, which is collected from chimney filters in coal-fired power plants, is composed of vitreous silica, alumina, iron oxide and lime. They can be used as a partial substitute for clinker and thus help to reduce CO2 emissions. |
Lafarge expertise results in safe waste solutions |
|
The use of waste products cannot be improvised. Lafarge has implemented stringent quality control standards as well as a training policy for its engineers, technicians and foremen. In this way, it is reinforcing the use of alternative fuels and materials while controlling industrial processes. The Group's R&D teams are also making an active contribution in this respect. The cement business considers the use of alternatives and the pursuit of industrial ecology to be separate but complementary parts of its core business. The business has developed a highly professional strategy as well as expertise and a dedicated organization at Group level and within operational units. The Group also establishes partnerships with local waste processing specialists. Lafarge has acquired share capital in Systech, a major waste management company in North America. |